Conclusion; with some small changes, this principle can work. The elastic can be attached tightly on the metal clips from the sheetmetal
dinsdag 25 april 2017
DIY context
Consult 25/04 3 concepts
DIY
- Thickness: the same everywhere
- Snap connection for the ribs
- Nest well!!!
- Optional ribs in the middle
- Rethink about the handle: hard, but flexible (maybe flexible silicon tube)
shops: Euroshop, Gamma, Brico, Action
MEDIUM
- The dimple is not possible --> better just a hole with a plastic insert: 12mm eyelets
- The attaching lips need to be tested: check
- Coating: powder coating or two component coating
http://www.protechantislipcoatings.com/?gclid=CjwKEAjw85DIBRCy2aT0hPmS1jkSJAC1m9UvrKCRWOfqPULHc9IH3s-nmDHeoBKbFqIkLxYLK96J6hoCc3rw_wcB
Better: https://www.verfwebwinkel.be/rust-oleum-supergrip-7100ns-antislip-coating-5-lit.html?gclid=CjwKEAjwutXIBRDV7-SDvdiNsUoSJACIlTqlhbYHN5D8x50roAaHUjWe2DuwQdFPbTFtWIqEhQyRthoCXq_w_wcB
- Thing aboat the finish of the rubber bands: we would add package with one long rubber band. Benefits: the user can decide in the beginning how long and how many of a specific lenght he needs. This gives him maximum freedom for the decision. Also, it's sheaper. We don't think the ends will come out because there's a tight fit. For the finishing of the cutted rubber bands, the user kan burn it easily.
MASS
- Material: rethink the material, is ABS the best solution?
- Material: choose one material for everything so it can be made and recycled easily
- The handel can be made way easier, so not the injection molded one, but maybe an extrusion of a rope with a flexible tube around it
- Thickness: the same everywhere
- Snap connection for the ribs
- Nest well!!!
- Optional ribs in the middle
- Rethink about the handle: hard, but flexible (maybe flexible silicon tube)
shops: Euroshop, Gamma, Brico, Action
MEDIUM
- The dimple is not possible --> better just a hole with a plastic insert: 12mm eyelets
- The attaching lips need to be tested: check
- Coating: powder coating or two component coating
http://www.protechantislipcoatings.com/?gclid=CjwKEAjw85DIBRCy2aT0hPmS1jkSJAC1m9UvrKCRWOfqPULHc9IH3s-nmDHeoBKbFqIkLxYLK96J6hoCc3rw_wcB
Better: https://www.verfwebwinkel.be/rust-oleum-supergrip-7100ns-antislip-coating-5-lit.html?gclid=CjwKEAjwutXIBRDV7-SDvdiNsUoSJACIlTqlhbYHN5D8x50roAaHUjWe2DuwQdFPbTFtWIqEhQyRthoCXq_w_wcB
- Thing aboat the finish of the rubber bands: we would add package with one long rubber band. Benefits: the user can decide in the beginning how long and how many of a specific lenght he needs. This gives him maximum freedom for the decision. Also, it's sheaper. We don't think the ends will come out because there's a tight fit. For the finishing of the cutted rubber bands, the user kan burn it easily.
MASS
- Material: rethink the material, is ABS the best solution?
- Material: choose one material for everything so it can be made and recycled easily
- The handel can be made way easier, so not the injection molded one, but maybe an extrusion of a rope with a flexible tube around it
maandag 24 april 2017
Concept MASS production CAD
The panel is injection molded ABS with ribs on one side, to make the panel stronger and protect the spanners.
The spanners are also injection molded parts out of ABS.
Handle: cilinder that can be folded open en where you can put one or two ropes in
On the rope, we attach a s-hook:
To attach the panels on each other, we will make elastics like this
Concept MEDIUM production CAD
Panels: sheetmetal, holes are lasered, edges en notches are bend
Panel with slots where you can put the rubber bands under to create a structure of tools |
zondag 23 april 2017
Sheet metal design guidelines stamping
Source: http://www.qualitytool.com/resources/Design-Handbook-Rev3.pdf
Notches and Tabs: should not be narrower than 1.5X the material thickness. Length of notches
can be up to 5X length of material thickness. That's why we can't use the system for the attaching pieces like in the DIY, because there's too much detail
Cutoffs:
There are three kinds of cutoffs in blanking: straight/square, half round or partial radius and full
radius. The square cutoff is the most economical. The full radius is not recommended as it
leaves an unavoidable “feather edge” burr along the outside material edge.
Piercing:
Holes: Minimum diameter of holes should be equal or greater than 1.2 X material thickness, and
2X material thickness for stainless steel or high tensile materials.
Edge-to-hole: Allow 2x material thickness (“web”) to prevent bulging of material
Forming:
Guidelines are similar to CNC press brake:
Bend Relief: Provide bend relief along L shaped features (Width=2*T and Depth=T +R)
Edge bulging: restrictive tolerances on V bends may result in edge bulging—provide bend relief
accordingly.
Hole-to-form: distance from hole-to-form—to avoid hole distortion, place holes no less than 2.5
times the material thickness + bend radius from the bend itself. (we have holes next to a bend, but the tollerances of the holes are not so important. So we can take account with it, but it's not necessairy)
Slot-to-form: long slots should be spaced 4 X the material thickness plus the bend radius.
Bead: depth = max. 3*thickness
Drawing:
Shapes: A myriad of shapes can be formed through multiple draws. Round shapes offer that
greatest ease and economy in drawing. Then next best option is square with adequate corner
radii. Costs increase for combinations of basic shapes and irregular shapes.
Radii: To facilitate drawing, keep radii as generous as possible: punch and die radius should be a
minimum of four times the material thickness. The part radius should be at no less than six times
the material thickness with appropriate drawing-quality material.
Another good source: file:///C:/Users/Lucas/Downloads/sheetmetal_guidelines1.pdf
vrijdag 21 april 2017
Task management till deadline 25/04
To obtain max efficiency, we allocated one production volume (diy, medium or mass) per member of the team.
The big guidelines are settled. The person will elaborate that specific production volume in detail. So he has to decide on his context what's the best solution without consultation of the other. This again, to have max efficienty.
Mass production: Maarten
Medium production: Lucas
DIY: Alex
The big guidelines are settled. The person will elaborate that specific production volume in detail. So he has to decide on his context what's the best solution without consultation of the other. This again, to have max efficienty.
Mass production: Maarten
Medium production: Lucas
DIY: Alex
donderdag 20 april 2017
Exploration small pieces for the rubber bands


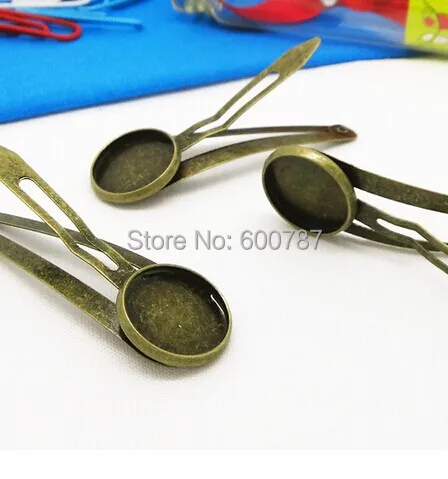
vrijdag 7 april 2017
Idea for hinge - the medium batch
The circular lips (above and below) are to push on with your finger so the 2 circular plates break up. This way, you can put the another pair op circular lips inbetween. Then, you can put a metal bar through te holes.
It is also possible to put 3 op them together.
It is made op stainless steel. Production technique: sheet metal folding.
Something to work on: can it be made strong enough?
woensdag 5 april 2017
DIY hinge further exploration
Abonneren op:
Posts (Atom)